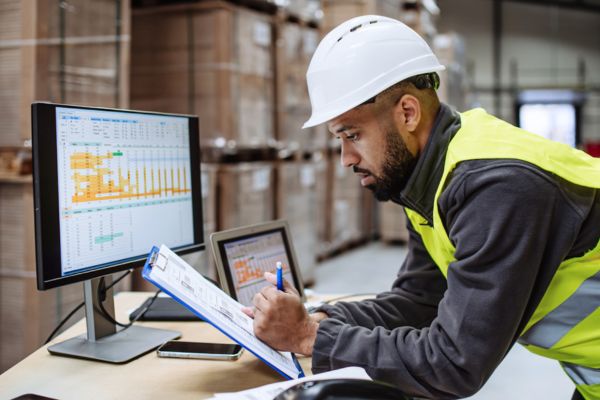
Das Lager und die Logistik gehören noch immer zu den Arbeitsplätzen mit dem höchsten Unfallrisiko. Ganze 83.098 meldepflichtige Unfälle ereigneten sich 2021 bei der Arbeit mit und in Lagereinrichtungen in Deutschland. (Quelle: DGUV) Es gilt also, im Bereich Arbeitssicherheit im Lager genau hinzuschauen – und Gefahrenquellen zu erkennen.
Inhaltsverzeichnis:
- Gefahrenquellen in Lager und Logistik
- Die Gefährdungsbeurteilung
- Das STOP-Prinzip
- So können Sie die Sicherheit im Lager verbessern
- enviropack: Arbeitsschutz beim Verpacken
Gefahrenquellen in Lager und Logistik
Paletten, Hochhubwagen oder hohe Regale: Das Sicherheitsrisiko ist in Lager und Logistik generell erhöht. Die Gefahrenquellen im Lager lassen sich in drei Bereiche einteilen:
- Entzündliche oder explosive Gefahrenquellen:
- Gefahrguttransporte
- Gefahrstofflager
- Chemikalien
- Gasbetriebene Anlagen
- Elektrische Gefahrenquellen:
- Ladestationen
- Kurzschlüsse
- Defekte Leitungen
- Mechanische Gefahrenquellen:
- Flurförderzeuge
- Hubtechnik
- Fördertechnik
- Werkzeuge
- Fehlende / falsche Schutzkleidung
- Falsch gesicherte bewegliche Teile
- Scharfkantige Oberflächen
- Regale, Paletten
- Rampen, Leitern
Zu den häufigsten Unfallursachen gehören:
- Herunterfallende Güter
- Unfälle mit Flurfördermitteln
- Abstürze von Gerüsten oder Leitern
- Quetschungen beim Be- und ENtladen
- Überlastungserscheinungen
Die Gefährdungsbeurteilung
Noch lange bevor im Lager überhaupt gearbeitet werden darf, muss eine Gefährdungsbeurteilung durchgeführt werden. Sie ist die Grundlage für ein umfassendes Sicherheitskonzept, das bereits parallel zur Lagerplanung erstellt werden muss.
Das gehört zum Sicherheitskonzept:
- Die Einrichtung
- Arbeitsplätze und -geräte
- Arbeitsabläufe
- Schulungen
- Ausrüstung
Bei der Gefahrenbeurteilung wird das komplette Lager auf mögliche Gefahrenquellen überprüft – und diese dann anhand eines einheitlichen Maßstabs beurteilt. Dabei geht es nicht nur um körperliche, sondern auch um psychische Auswirkungen der Arbeit im Lager.
Das STOP-Prinzip
Um etwaige Gefahrenquellen sofort anzugehen, hat sich das STOP-Prinzip bewährt. Es soll in vier Schritten die Arbeitssicherheit im Lager erhöhen. Wichtig: Die Reihenfolge der Schritte darf nicht verändert werden.
- Kann die Gefahrenquelle ersetzt werden? (Zum Beispiel durch ein anderes Verfahren, eine andere Maschine oder einen anderen Rohstoff)
- Kann die Gefahr eingedämmt werden? (Zum Beispiel durch technische oder bauliche Anpassungen)
- Kann die Gefahr durch Veränderungen im Arbeitsablauf verringert werden?
- Kann eine passende Schutzausrüstung vor der Gefahr schützen?
So können Sie die Sicherheit im Lager verbessern
Je nach Unternehmen und Lagerfläche sind Verbesserungen im Bereich Arbeitssicherheit sehr individuell. Trotzdem gibt es einige Bereiche, die nahezu jedes Lager betreffen.
Regalsysteme
Tragfähigkeit und Standfestigkeit sind die wichtigsten Faktoren, wenn es um die Sicherheit der Regale im Lager geht. Die zulässigen Fach- und Feldlasten dürfen nicht überschritten werden, die Last muss gleichmäßig verteilt sein.
Wichtig: Gewerblich genutzt Regale müssen regelmäßig in speziellen Sicherheitskontrollen überprüft werden.
Flurförderzeuge
Stapler und Hubwagen brauchen ausreichend Platz zum Fahren und Manövrieren. Achten Sie deshalb darauf, dass noch genug Abstand zum Regal eingehalten werden kann und die Arbeitsgangbreite ausreicht.
Zusätzlichen Schutz bieten Anfahr- und Rammschutz. Sie verhindern, dass Regale bei Fahrfehlern umkippen – und machen das Lager noch sicherer.
Ebenfalls wichtig: Inspizieren Sie alle verwendeten Fahrzeuge regelmäßig und sorgen Sie für eine regelmäßige Wartung. Dazu gehören Prüfungen wie z.B. die FEN-Prüfung, aber auch tägliche Sichtüberprüfungen.
Ladungssicherung
Ladungssicherung ist aus zwei Gründen wichtig: Sie schützt einerseits Ihre Mitarbeiter, aber auch die Ware selbst. Ganz nebenbei ist die korrekte Ladungssicherung für bestimmte Situationen sogar vorgeschrieben.
Zur richtigen Ladungssicherung gehören:
- Warnhinweise und Etiketten
- Passende Materialien
- Sichere Verpackungen
- Stabiler Untergrund (dazu z.B. ein Rammschutz)
- Rückwandgitter
- Durchschubsicherungen
- Endständerrahmenerhöhung (gegen seitliches Überkippen)
Zeitmanagement
Noch immer geschehen viele Arbeitsunfälle aufgrund von Hektik und Zeitdruck. Erstellen Sie deshalb einen realistischen Zeitplan, der auch wirklich eingehalten werden kann. Das verringert die Fehleranfälligkeit und somit die Unfallgefahr.
Moderne Technologien wie Pick-by-Vision oder eine effizienten Lagerausstattung sorgen außerdem dafür, dass die Gefährdung im Lager kleiner wird – ohne Arbeitszeit zu verlieren.
Hilfsmittel
Die Arbeit im Lager ist mitunter körperlich sehr belastend. Stellen Sie Ihren Mitarbeitern deshalb ausreichen Hilfsmittel zum Verpacken und zum Transport zur Verfügung.
Das spart einerseits Kraft und verringert das Risiko von Unfällen oder Überlastungserscheinungen – es macht auch den gesamten Arbeitsprozess schneller und effektiver.
Kennzeichnung
Etwaige Risiken oder Gefahrenbereiche müssen für alle Arbeiter im Lager auffällig und ordnungsgemäß gekennzeichnet sein. Dazu gehören beispielsweise Bereiche, in denen Gabelstapler fahren, Zugangsbeschränkungen oder andere Beschilderungen.
Doch nicht nur das: Auch Handhabungshinweise an Lagergut sind wichtig. Vor allem, wenn es sich um Waren mit einem erheblichen Gefahrenpotential handelt.
Schulungen
Alle Mitarbeiter müssen immer auf dem neuesten Stand sein, was die korrekte Anwendung der Maschinen oder Schutzausrüstung angeht. Achten Sie also darauf, dass Ihre Mitarbeiter stets über Neuerungen und Sicherheitsvorgaben informiert sind.
Regelmäßige Schulungen helfen dabei, altes Wissen aufzufrischen und Neues dazuzulernen.
Arbeitsplätze
Ein gut ausgestatteter und ergonomischer Arbeitsplatz soll dem Mitarbeiter die Arbeit erleichtern und gesundheitliche Risiken minimieren.
Vor allem Kommissionierstationen müssen sicherstellen, dass Arbeiter schnell, effizient und bequem arbeiten können. Höhenverstellbare Tische, hydraulische Arme oder ergonomische Arbeitsmaterialien gehören heutzutage zum Standard – und sind ein wichtiger Bestandteil im Gesundheitsschutz.
Ebenfalls gibt es ergonomische Klebebandsysteme, welche Ihre Mitarbeiter enorm entlasten. Wer den ganzen Tag Pakete packt weiß, welche Belastung auf den Handgelenken liegt. Das ergonomische Klebebandsystem ZeroTape sorgt für 75 % weniger Beanspruchung der Muskeln in Handgelenk, Arm und Schulter. ZeroTape Packbandsystem ➡️
Persönliche Schutzausrüstung (PSA)
Je nach Arbeitsbereich kann die Persönliche Schutzausrüstung individuell ausfallen.
Zur gängigen Schutzausstattung gehören meist:
- Helm oder Stoßkappe
- Sicherheitsschuhe
- Handschuhe
- Warnwesten
Die PSA sorgt dafür, dass alle Arbeiter schnell erkennbar sind und beispielsweise Kollisionen mit Fahrzeugen vermieden werden.
Sorgen Sie dafür, dass alle Bestandteile der Schutzausrüstung für alle Mitarbeiter schnell und unkompliziert auffindbar sind. Sonst laufen sie Gefahr, Arbeiten „nur kurz“ ohne passenden Schutz auszuführen – eine riesige Gefahrenquelle.
Inspektionen
Führen Sie regelmäßig Sicherheitsinspektionen an allen Lagersystemen durch. Gemäß der DIN EN 15635 sind Sie sogar zu einer jährlichen Technischen Inspektion der Regale (TIR) verpflichtet.
Dabei müssen alle Elemente aller Regalsysteme genau inspiziert und auf Schwachstellen überprüft werden.
Automatisierung
Die Technik erlaubt es uns, viele Teile der Lagerarbeit bereits zu automatisieren. Das verringert die Anzahl der Fehlerquellen und verbessert das Sicherheitsniveau im Lager erheblich.
Mögliche Bereiche für Automatisierung sind:
- Transportsysteme
- Kommissionierstrecken
- Lagersysteme
Ordnung und Sauberkeit
Lassen Sie Ihr Lager regelmäßig industriell reinigen, um alle Arbeitsbereiche sauber zu halten und für eine ausreichende Hygiene zu sorgen.
Industriell gereinigt werden sollten:
- Böden
- Wände
- Decken
- Regale
- Beleutungskörper
- Maschinen
- Abwasserrohre
Außerdem sollte Ordnung weit oben auf die Prioritätenliste für das Lager stehen – denn so sinkt einerseits das Unfallrisiko, andererseits steigt die Produktivität.
Vorbilder
Nicht zuletzt ist es wichtig, als Führungskraft mit gutem Beispiel voranzugehen und sich selbst an alle Regeln und Vorschriften zu halten. Nur dann können Sicherheitsbestimmungen im Lager auch langfristig umgesetzt werden.
Kurz gesagt: Was für den Arbeiter gilt, gilt auch für den Chef.
enviropack: Arbeitsschutz beim Verpacken
Arbeitsschutz im Lager ist wichtiger denn je. Bei enviropack finden Sie deshalb Materialien und Werkzeuge aus dem Verpackungsbereich, die die Kommissionierung und das Verpacken im Lager noch sicherer und einfacher machen.
Mit enviropack die Sicherheit im Lager erhöhen – das geht ganz einfach. Entdecken Sie jetzt unser Angebot.
Zuletzt aktualisiert am 19. Juni 2024 von Levana Brusius